
Blast Rooms – Blast Booths – Blast Cabinets
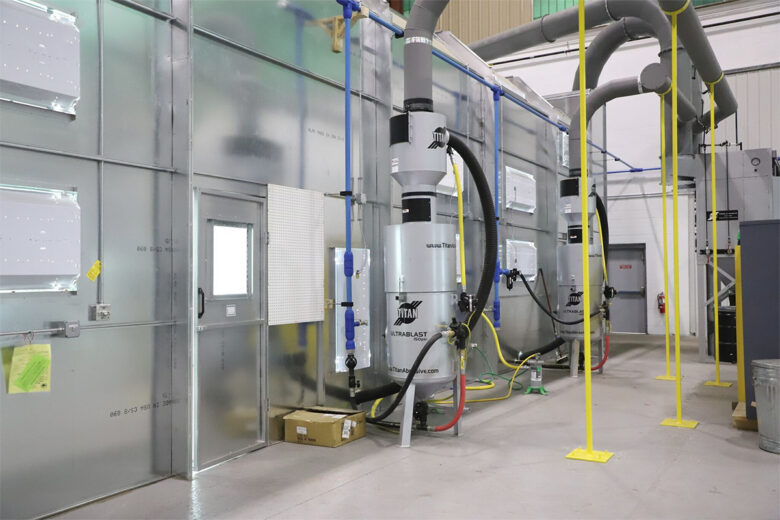
What is a blast room?
A blast room is a much larger version of a blast cabinet. Blast operators work inside the room, abrasive blasting the surfaces of objects to meet the needs of the finished product. Blast rooms come in many sizes, some of which are big enough to accommodate rail cars, commercial and military vehicles, construction equipment, and aircraft.
Each application may require the use of different pieces of equipment; however, several key components can be found in a typical blast room:
- The enclosure or room – A blast room is an enclosure designed to remain sealed to prevent blast media from escaping. Typically blast rooms contain lights, product entry/exit doors, and a personnel door.
- Blast equipment – An air blasting system that commonly consists of a blast machine (blast pot), which can be filled with various abrasive blasting medias.
- Media reclaim system – A media reclamation/recovery system that’s used to collect abrasive blasting media so it can be re-used. These can be pneumatic or mechanical (bucket elevator) systems, installed on or in the floor of the blast room.
- Dust collector – A dust collection system is the most important component of an abrasive blasting room. The dust collector filters the air in the room, allowing maximum visibility, safety for the blast operator, and prevention of particulate matter from escaping.
Additional equipment can be added for convenience and improved usability, such as HMI control panels, overhead crane slots, rubber lining, etc. To learn more about blast rooms, please see our Custom Blast Rooms page.
What’s the difference between a blast room, a blast booth, and a blast cabinet?
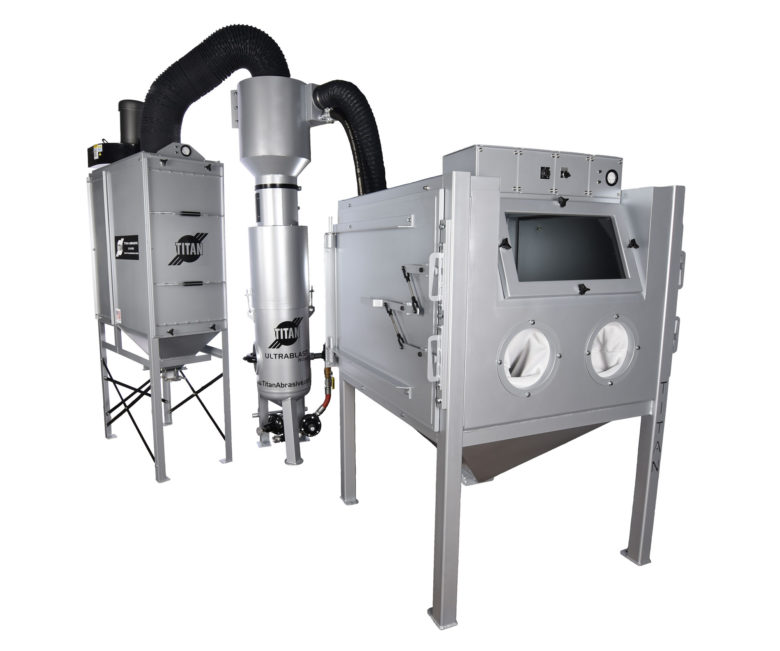
The terms “blast room,” “blast booth” and “blast cabinet” are often used interchangeably as they perform the same function. The difference between a blast room and a blast cabinet, however, is where and how the blast operator works.
Blast rooms, or blast booths, allow operators to work inside the enclosure; they’re protected from the abrasive media by heavy duty gear and an air fed helmet.
With blast cabinets — also referred to as “blast booths,” although this is technically incorrect — operators stand outside the cabinet. They operate the internal blast controls by inserting their arms into the gloves attached to glove holes on the cabinet, viewing the part to be blasted through a view window, and turning the blast on and off using a foot pedal.
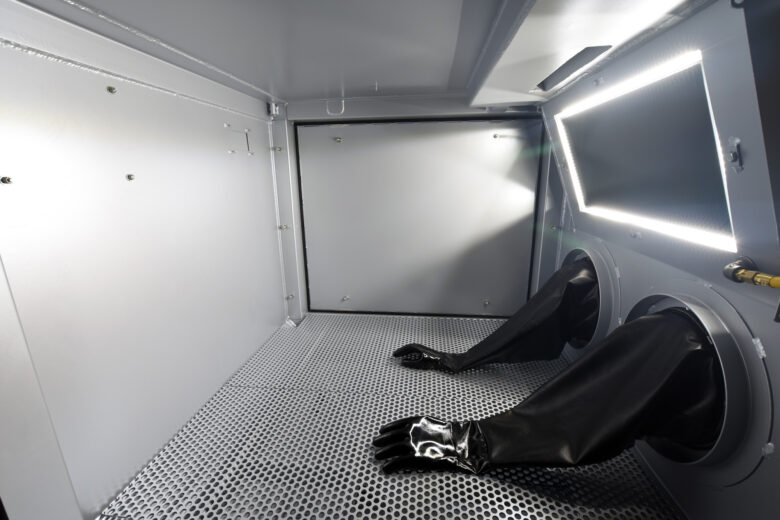
A blast cabinet usually consists of four components: the containment (cabinet), the abrasive blasting system or blast machine, the abrasive recycling system, and the dust collector.
Sandblasting cabinets are found on most shop floors. See our Blast Cabinets page for additional details about Titan’s line of high-performance industrial blast cabinets.
What are typical or standard blast room sizes?
Blast rooms can be custom designed and built based on the application. Some can be very large! Blast rooms also come in standard sizes, depending on the manufacturer. Titan Abrasive offers three, easy-to-install, standard-size blast room packages:
- 10’ x 10’ x 10’
- 10’ x 10’ x 15’
- 15’ x 10’ x 25’
See our Blast Room Packages page for details.
How much does a blast room cost?
It depends! For a custom engineered and built on-site blast room, we would provide you with a quote after talking with you about your particular application.
Our Blast Room Packages come as complete systems with fixed pricing (and therefore, can’t be customized). The packages include the media reclaim system, dust collector, and 6 cubic foot blast machine. See our Blast Room Packages for details.
How many man doors are required in a blast room?
It depends on the size of the blast room, the location, and the application. A standard size sandblast room typically has one personnel/man door; larger rooms can have two or more man doors. In addition, a blast room can have one entry / exit door, or it can have pass-through doors on either end, large enough to accommodate a forklift, vehicle, or very large assembly.
Which is better for heavy parts – a blast room or blast cabinet?
Because a blast room is exceedingly heavy, it requires a solid foundation of at least 6″ thick concrete. Consequently, a blast room has a floor capable of supporting the room itself and parts that can weigh as much as 10 tons.
Standard blast cabinets can’t hold nearly the same weight. If you’re going to be blasting heavy parts (i.e., over 1,000 lbs), you need to provide structural support to the cabinet.
The weight of your parts may necessitate the addition of a turntable so that the part can be spun around inside the cabinet to ensure all surfaces get blasted. Sometimes, a track extension is required as well, creating a small work cart on wheels.
Operators can slide the turntable out of the cabinet through the swing doors (or through an optional vertical sliding door), drop the part onto the turntable with a forklift or manually, and slide the part back inside.
See also: Seven Custom Options You Can Add to Your Titan Blast Cabinet
How large of a dust collector do I need? Or, what size dust collector do I need for my blast room?
The typical calculation for dust collector sizing is determined by the following formula:
Width of Room x Height of Room x Cross-Sectional Air-Speed (FPM) = C.F.M.
The cross-sectional airspeed is typically 50 f.p.m. for steel grit abrasive and 60 f.p.m. for non-ferrous mineral abrasives.
Do you sell blast room & blast cabinet dust collectors?
Yes! Our Cartridge Dust Collectors are the most affordable high-performance dust collectors on the market today and have been designed exclusively for abrasive blasting applications. Since our dust collectors are modular, no job is too big or too small.
A great deal goes into building an abrasive blast room, from determining the size of the room, to properly configuring the dust collection and media recovery systems. Let Titan Abrasive and our 70+ years of experience design the perfect system to suit your specific needs and maximize your ROI. Contact Us today for a free quote.
Brandon Acker: President
Brandon purchased Titan Abrasive from his uncle and founder in 2013. Titan has since redesigned its entire product line to solve dozens of industry challenges.
Brandon purchased Titan Abrasive from his uncle and Titan founder, Bruce Maurer, in 2013 after spending five years learning the ins and outs of the business. He and VP of Engineering Brian Fox have completely redesigned the entire product line to solve the dozens of challenges that have plagued the blasting industry for decades.
Brandon is passionate about American manufacturing, the jobs it creates, the quality produced, and the bright future that lies ahead. He’s a frequent guest on manufacturing podcasts where he shares his deep industry expertise. Brandon holds a Bachelor of Science degree from Arizona State University.